خوردگی دیگ بخار
خوردگی دیگ بخار
آب های طبیعی در اثر تبخیر، رسوباتی را بر جا می گذارند که موجب خوردگی دیگ بخار و بروز مشکلاتی می گردند. همچنین این گونه آب ها می توانند خوردگی سطوح دیگ های بخار را شامل شوند. این مشکلات علاوه بر متوقف شدن سیستم و لزوم به تعویض قطعات موجب افزایش هزینه های گوناگون می گردند. بطور کلی استفاده از آبی عدم منطبق با استاندارد های کیفیت آب دیگ بخار در دیگ های بخار مشکلات زیر را به وجود می آورد :
- تشکیل رسوب بر جداره دیگ بخار (Scaling)
- خوردگی سطوح دیگ بخار (Corrosion)
- حمل قطرات مایع توسط بخار(Carryover)
- کف کردن (Foaming)
- غلغل کردن (Priming)
- شکنندگی قلیایی فلز دیگ بخار (Coustic priming)
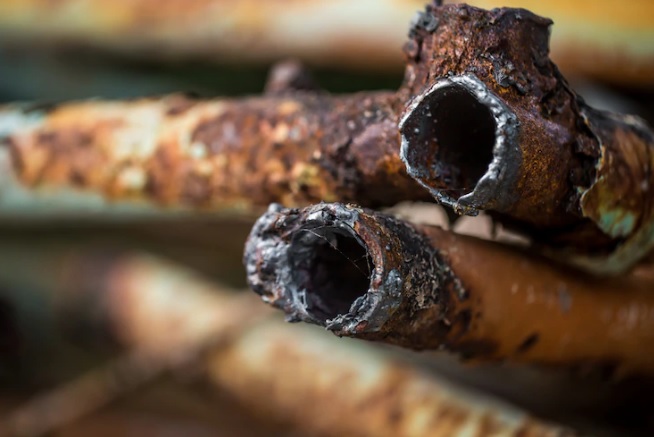
عوامل زیادی از جمله: ساختمان، فشار دیگ بخار، مقدار تولید بخار و شیوه بهره برداری، در میزان ایجاد مشکلات سهم مؤثری دارند.
مکانیسم تشکیل رسوب
در اثر وجود املاح محلول در آب سه حالت مختلف رسوب در دیگ بخار تشکیل می گردد.
- رسوبات نرم که به جداره ها نمی چسبند.
- رسوبات نیمه سخت که به جداره ها می چسبند ولی به آسانی جدا می گردند.
- رسوبات بسیار سخت که چسبندگی زیادی دارند و به آسانی از جداره جدا نمی گردند.
رسوبات نوع سوم در دیگ های بخار ایجاد مشکل می کنند، بنابراین لازم است آب به شیوه ای تصفیه گردد که بتواند آب مناسب جهت تغذیه آب دیگ بخار را فراهم کند و درون دیگ رسوب ایجاد نشود.
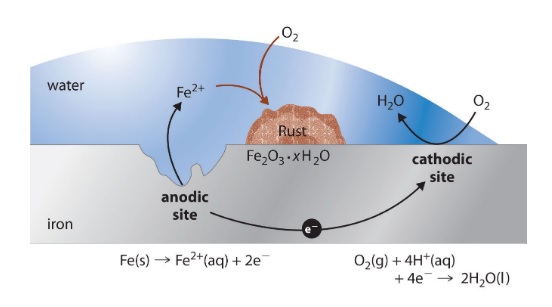
ایجاد رسوب درون دیگ بخار به دو دلیل عمده زیر می باشد:
- تغییر در کیفیت شیمیایی آب به هنگام ورود در دیگ بخار: در این فرایند کلسیم بیکربنات که دارای حلایت زیادی است به کلسیم کربنات که دارای حلالیت بسیار کمی است، تبدیل می شود و رسوب می نماید.
- کاهش حلالیت املاح موجود در آب به دلیل افزایش دما: تغییر دما در مکانهای مختلف یک سیستم موجب می شود که در اثر بالا بردن دما در مجاورت سطوح دیگ بخار املاح موجود به صورت فوق اشباع درآیند و کریستال های رسوب تشکیل شوند و نیز در صورت ایجاد هسته های اولیه، رسوبات روی سطوح فلز دیگ بخار ته نشین می گردند.
به طور کلی برای ته نشین شدن املاح موجود در آب شرایط زیر لازم می باشد.
- فوق اشباع شدن: مهمترین شرایط برای تشکیل رسوب فوق اشباع بودن محلول است. تغییرات در دما، فشار، PH، تبخیر و تلغیظ از جمله عوامل به وجود آمدن یک محلول فوق اشباع می باشند. آب ورودی به دیگ های بخار که در مجاورت جداره های گرم دیگ قرار می گیرد پس از مدتی به صورت فوق اشباع در می آید زیرا با بالا رفتن دما در این ناحیه حلالیت کاهش مییابد ولی در نواحی دور از جداره ها این پدیده روی نمی دهد.
تشکیل رسوب بر روی دیواره داغ لوله ها داغ و خوردگی دیگ بخار - ایجاد هسته های اولیه: وجود هسته های اولیه موجب تشکیل ذرات رسوب می گردد. عوامل مختلفی مانند ذرات گرد و غبار، رسوبات قبلی، ذرات ایجاد شده از خوردگی و غیره می تواند به عنوان هسته های اولیه ایجاد رسوب عمل کنند.
- زمان تماس: پس از فوق اشباع شدن محلول و ایجاد هسته های رسوب، برای رشد ذرات و ته نشین شدن آن ها به فرصت کافی نیاز می باشد.
ترکیبات کلسیم، منیزیم، آهن، مس، آلومینیوم و سیلیس از عوامل رسوب کننده مهم در آب تغذیه دیگ های بخار می باشند. این رسوبات به دو حالت ممکن می باشند.
- رسوبات کریستال شده بر روی سطح
- رسوبات لجنی بدون شکل و غیر یکنواخت
در شکل زیر دو نمونه از رسوب و چگونگی تشکیل رسوب نشان داده می شود.
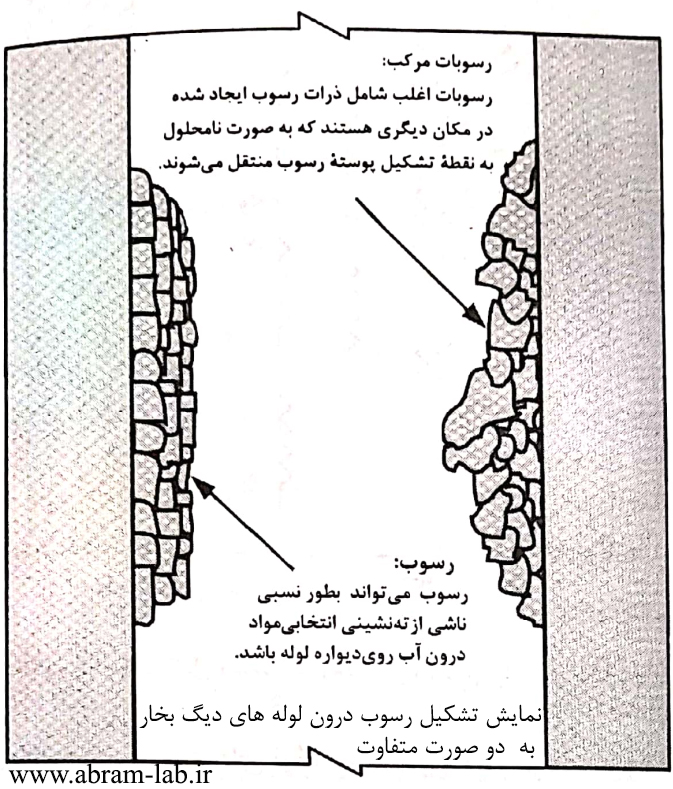
مشکلات حاصل از تشکیل رسوب در دیگ های بخار
ایجاد رسوب در جداره دیگ های بخار دو اشکال عمده به وجود می آورد که عبارت اند از:
- رسوبات حاصل از املاح موجود در آب تغذیه دیگ های بخار مانند یک لایه عایق عمل می کنند و انتقال حرارت را به مقدار قابل توجهی کاهش می دهند. ساختمان رسوب، خلل و فرج موجود در آن ها، ضخامت لایه رسوب بر روی دیواره و شرایط دیگ بخار در مقدار اتلاف حرارت مؤثر می باشد. این رسوبات به دلیل کاهش میزان انتقال حرارت از قدرت تولید بخار می کاهد و موجب پایین آمدن راندمان دیگ های بخار می گردد یا به عبارت دیگر مصرف انرژی برای تولید میزان مشخص بخار را افزایش می دهد.
- رسوبات دیگ بخار موجب کاهش انتقال حرارت و افزایش بیش از حد دمای فلز می گردد که در نتیجه باعث تخریب ساختار فلز و در نهایت ترکیدن آن می شود. بدیهی است حساسیت دیگ های بخار مدرن که میزان انتقال حرارت در آنها بالا است بیشتر می باشد. ضریب انتقال حرارت برای رسوبات مختلف متفاوت است. این مقدار برای رسوبات کلسیم کربنات بیشتر است. خلل و فرج موجود در رسوبات نیز ضریب انتقال حرارت را تغییر می دهد. اگر این خلل و فرج ها توسط گاز پر شوند انتقال حرارت به مقدار قابل توجهی کاهش می یابد. میزان خلل و فرج موجود در رسوبات نیز به درجه فوق اشباع بودن، هسته های اولیه، دما، فشار و شرایط محیطی بستگی دارد. اگر رسوب گذاری سریع باشد رسوبات، متخلخل، نرم و غیر چسبنده می باشند. رسوبات با گذشت زمان سخت تر و چسبنده تر می گردند.
خوردگی در دیگ های بخار (Boiler,s corrosion)
جلوگیری از خوردگی دیگ بخار و دستگاه های جانبی آن یکی از دلایل پر اهمیت کنترل آب دیگ بخار است. دلیل اصلی خوردگی دیگ های بخار به عوامل زیر بستگی دارد.
- مقدار نامناسب اکسیژن
- pH نامناسب
- وجود یونهای نامناسب.
- وجود گازهای محلول.
- میزان بالای مواد محلول( TDS بالا).
- قلیائیت نامناسب.
- میزان سیلیس زیاد.
در اینجا لازم است ابتدا لایه های نازک اکسیدها که به نام فیلم های اکسیدی در نتیجه فرآیندها تشکیل یافته اند مورد بررسی قرار گیرند.
1- خوردگی آهن در آب در شرایط عدم حضور اکسیژن
با توجه به اینکه پتانسیل آهن در آب در شرایط عدم حضور اکسیژن از پتانسیل هیدروژن در جدول اکسیداسیون و احیاء پائین تر می باشد بر طبق واکنش زیر خورده می شود.

در آب خالص محصول خوردگی فروهیدروکسید (2(Fe(OH) می باشد که به –OH و ++Fe هیدرولیز می شود و موجب افزایش pH سیستم می گردد و نیز تولید رسوب در سطح فلز می نماید. افزایش درجه حرارت و شرایط محیط موجب تشکیل فیلم محافظ مگنتیت Fe(OH) بر روی سطح فلز می شود که به مقدار بسیار زیادی از خوردگی آهن جلوگیری به عمل می آورد.
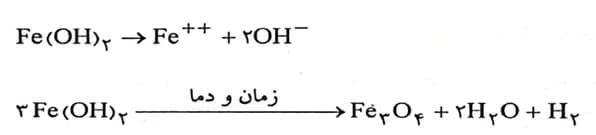
آزمایش های انجام شده نشان می دهد که در بالاتر از دمای C ° ۱۲۰ فقط مگنتیت موجود می باشد.

2- خوردگی آهن در آب در شرایط حضور اکسیژن
فروهیدروکسید که بر طبق بررسی بالا تشکیل می شود با حضور اکسیژن ناپایدار می باشد و به فریک هیدروکسید تبدیل می گردد. تجربه نشان داده است که معمولاً بدون کنترل شیمیائی دقیق در این شیوه خوردگی بیشتر می شود و به طور خلاصه واکنش آهن، آب و اکسیژن را می توان به صورت زیر خلاصه کرد.

فریک هیدروکسید به طور محسوسی در آب غیر محلول می باشد و لذا روی سطح فلز رسوب می کند در ضمن این رسوب خاصیت حفاظتی ندارد و در اثر مرور زمان و درجه حرارت به آلفا فریک اکسید(3O 2 Fe- α ) قرمز رنگ که محصول نهایی خوردگی می باشد تبدیل می گردد.

لازم به تذکر است که نباید هماتیت (3O 2 Fe- α ) را با 3O 2 Fe- γ که لایه محافظی است اشتباه نمود. خوردگی توسط اکسیژن و تشکیل هماتیت با ایجاد حفرهای آبله گون[1] مشخص می گردد. کاهش pH ، سرعت خوردگی را همراه با افزایش بیشتر حفره ها و نیز رشد آنها تشدید می کند. در صورتی که افزایش pH و شرایط مناسب موجب تشکیل فیلم اکسید محافظ سیاه رنگ مگنتیت[2] (4O 3 Fe ) می گردد.
همچنین شرایط مطلوب آب در pH حدود هفت و میزان کنترل شده اکسیژن تشکیل فیلم اکسید (در حدود ppb ٢٥٠ – ١٥٠) موجب تشکیل فیلم محافظ 3O 2 Fe- γ می گردد.
معمولاً در مورد خوردگی از نوع اکسیژن سطح فلز زمانی فعال می گردد که اکسید سیاه رنگ احیاء شده[3] در داخل حفره وجود داشته باشد و اطراف حفره ها از فریک اکسید قرمز رنگ تشکیل شده باشد. بنابراین وجود اکسید سیاه رنگ داخل حفره نشان دهنده فعال بودن واکنش خوردگی می باشد و نیز اکسید آهن قرمز رنگ در داخل حفره مبین این نکته می باشد که خوردگی در داخل حفره متوقف شده و فعال نمی باشد.
آزمایش های مختلف نشان می دهد که در°C ۱۰۰ فروهیدروکسید به 3O 2 F و 2H و در°C ۲۰۰ ترکیب γ – FeOOH با از دست دادن آب به 3O 2 Fe- γ تبدیل می گردد.
پژوهشگران زیادی در مورد لایه های اکسیدی تشکیل شده بر روی آهن در آب و در درجه حرارت های مختلف با مقادیر مختلف اکسیژن محلول مطالعه کرده اند. نتیجه های حاصل شده توسط میکروسکوپ های الکترونی و دستگاه پراش اشعه ایکس [4]نشان می دهد که فیلم های تشکیل شده شامل γ – FeOOH به رنگ زرد مایل به نارنجی و محصول خوردگی معمولی( 2O H3 ، 3O 2 Fe ) می باشد. در درجه حرارت های بالا، فیلم های اکسیدی تشکیل شده شامل فیلم محافظ سیاه رنگ 4O 3 Fe و فیلم محافظ قهوه ای پر رنگ 3O 2 Fe- γ و 3O 2 Fe- α به رنگ قرمز آجری می باشد. فیلم 3O 2 Fe- α تا حد کمی دارای خاصیت مغناطیسی می باشد و حضور این فیلم دلیل بر خوردگی در حضور اکسیژن محلول می باشد.
3- فیلم های اکسیدی تشکیل شده بر روی آهن در هوا
پژوهشگران در مورد تشکیل فیلم های اکسیدی بر روی آهن در هوا و درجه حرارت کمتر از °C ۲۰۰ بر این عقیده اند که فیلم های اکسیدی تشکیل شده شامل اکسیدهای 3O 2 Fe- γ و 4O 3 Fe با ساختمان کریستالی از نوع مکعبی اسپینل و در درجه حرارت بالاتر از°C ۲۰۰ اکسیدهای تشکیل شده شامل اکسیدهای زیر می باشند:

لازم به ذکر است که 3O 2Fe- α در روی 4O 3 Fe و یا 3O 2Fe-γ تشکیل می گردد. نسبت درصد و ضخامت این فیلم های اکسیدی به شرایط اکسیداسیون و آماده سازی سطح، حضور ناخالصی ها در آهن و ترتیب و جهات کریستالی[5] بستگی دارد.
ترتیب تشکیل اکسیدهای ایجاد شده بر روی سطح به حالت زیر می باشد:

[1]– Reduced Black Oxide
[2] -X-Ray diffraction
[3] – Tubercolous
[4] – Magnetite
[5] – Crystal Orientation
نظرات بسته شده است.